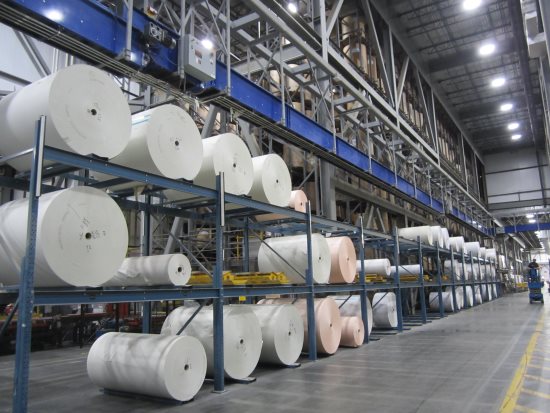 | | Giant rolls of paper Photos Vera Kochan | | | | | | Few people realize the hard work and time consuming effort it takes to produce a newspaper. From the conception of an article to the final process of delivery, keeping the public informed and up-to-date is an ever-changing challenge.
This reporter recently toured Bay Area Production Services, a Fremont-based newspaper printing facility which is owned by the San Francisco Chronicle, a Hearst Corporation, that prints the Lamorinda Weekly among other newspapers.
The first stop in the massive warehouse-like facility that employs approximately 100 personnel, was to view the area where gargantuan rolls of white paper, resembling adding machine tape for the Jolly Green Giant's calculator, stood stacked on floor-to-ceiling racks. The paper comes straight from the mill and incorporates recycled product. Paper sizes have minor variances from roll to roll, but for the most part they arrive cut to fit standard newspapers. This section is run with little to no human interference as electronic sensors determine when rolls need to be replaced during printing.
Across from the stacks of paper rolls are enormous vats containing ink. The same color spectrum used in a Laser Jet Printer - cyan, magenta, yellow and "key" (black) - are used to print the wording and pictures in a newspaper. According to Bay Area Production Services CSR & Receiving and Logistics Manager Rocky Dave, "This facility began using color in newspapers about 10 years ago."
Next in the process came the visit to a room with consoles resembling something from Mission Control at NASA. Publishers from various newspapers transmit mock-ups of a completely corrected and edited edition to a BAPS console where the content is checked one last time before the paper "goes to press."
Aluminum printing plates are etched by lasers to resemble the printed pages of a newspaper. The printing plates are then mounted onto the printing press. Ink is added in the actual printing process. Each prospective newspaper page is lasered onto four different printing plates; one plate for each color of ink. Because each printing plate has been marked by lasers, no plate is used twice.
The print plates are then mounted onto web offset presses, so called because they use giant reels or "webs" of newsprint and four colors of ink. The machines were designed to print thousands of copies an hour. "Our presses can print up to 80,000 copies per hour," Dave stated. "If the web breaks the paper tears during the run."
The ink is stacked in "towers." Each tower level contains a different color of ink. The four printing plates add the different color levels to the paper, essentially layering ink until it creates the finished product.
The separate webs of paper then come together and are slit, cut again, folded and individually sent along on conveyor belts high above the floor much like small, winding roller coasters zooming overhead. This sight is the climax of the tour, because thanks to the movies and television, it's the one process most people think of at the mention of printing newspapers.
At the end of "the ride" the individual issues are stacked and packaged at the distribution center where they are broken down into zip and area codes prior to being fork-lifted on pallets to loading bays for delivery. The whole process is so fast - it can take less than a minute from putting ink onto paper to the final step of ready for pickup.
When asked whether the term "Stop the presses" is still used, even in this highly mechanized form of printing, Dave replied, "Yes, it can happen. We have people stationed in critical areas, and the turn around time to resume printing is usually 10 minutes." |